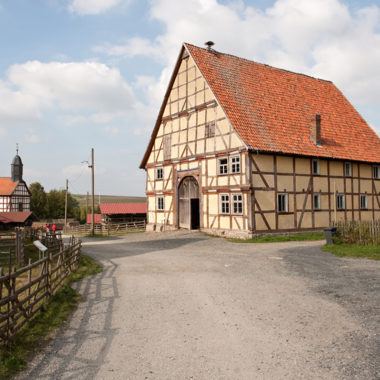
Indigo-Dyeing
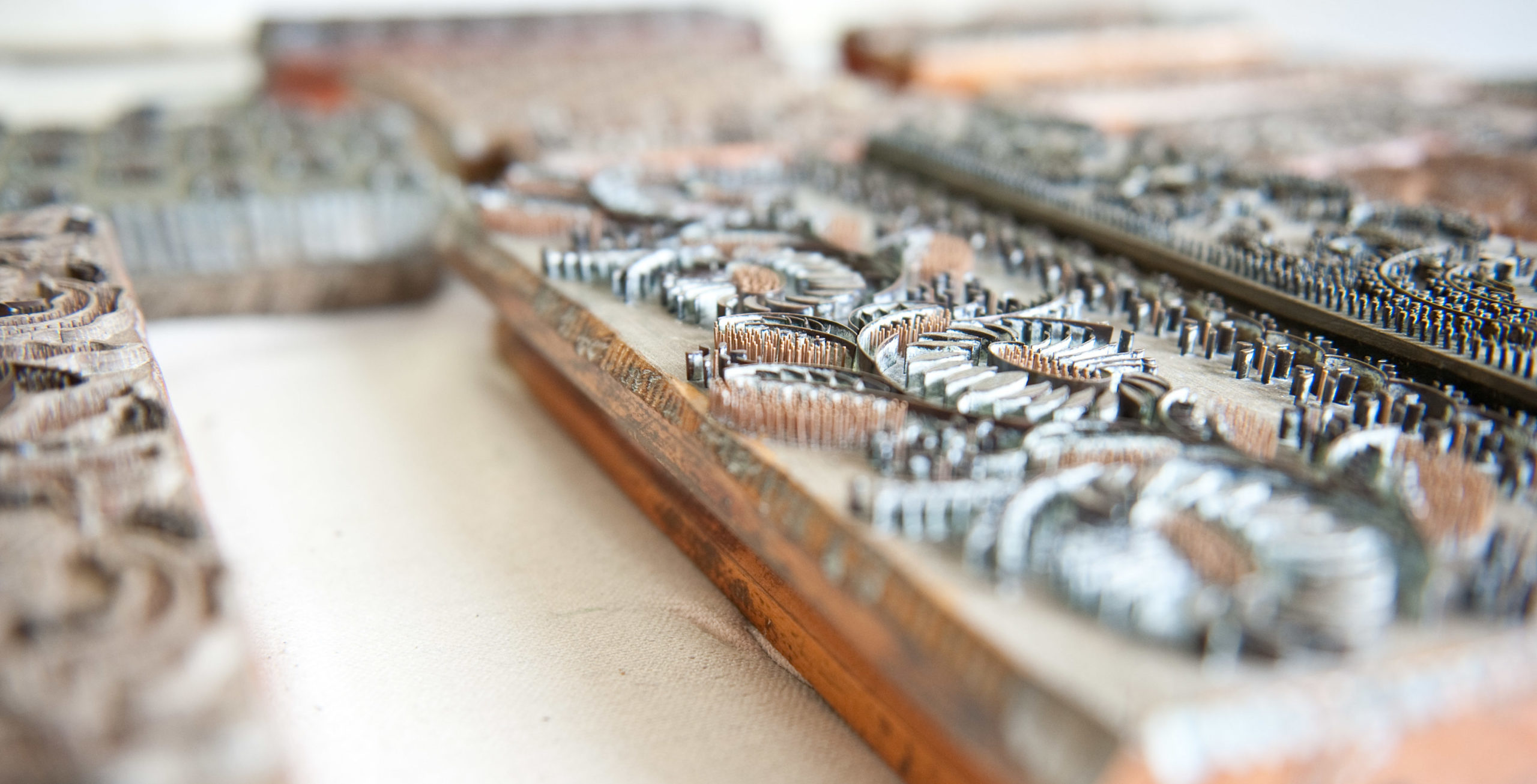
Originally, the blue dye was extracted from the woad plant, but indigo, a dye yielding better results, had begun to replace it in the 16th century. A mix of indigo and woad resulted in a more lasting blue than indigo alone. Reserve printing arrived in Europe from Asia in around 1690 and replaced direct printing. In reserve printing, the textile is first printed and then dyed, with the printed pattern being reserved from the dye. The patterns are printed on the cloth using print blocks. The variety and quality of its blocks were a dye-shops pride and joy, and textiles were usually printed to order. To print, the block is dipped into a printing liquid, the paste, and then pressed onto the fabric. The recipes for making this paste were often a closely guarded secret of the workshops. The printed fabric is then folded in a particular manner and immersed into the dye vat several times. The blue colour, however, is the result of drying and oxidation. The dye-rejecting paste can then be washed out, and the printed pattern appears white against a blue background. The invention of chemical dyes in the second half of the 19th century as well as the invention of industrial printing and the decline in the popularity of traditional dress finally led to the decline of indigo-blue dyeing in Hesse.
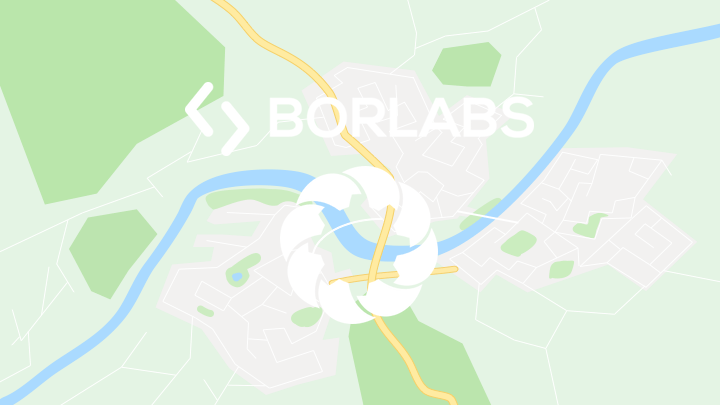
Mit dem Laden der Karte akzeptieren Sie die Datenschutzerklärung von Google.
Mehr erfahren
More links
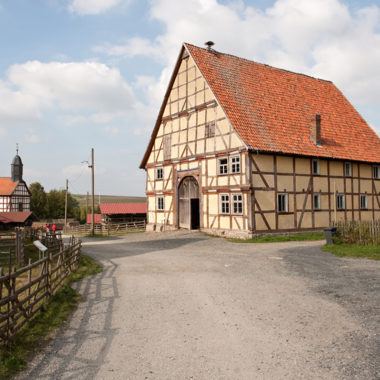