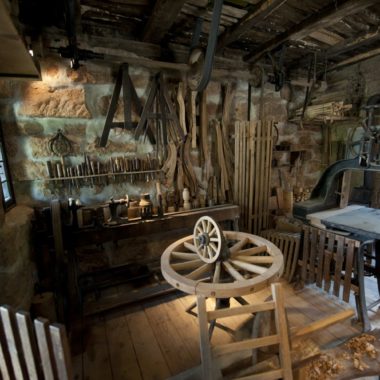
Wheelwrights
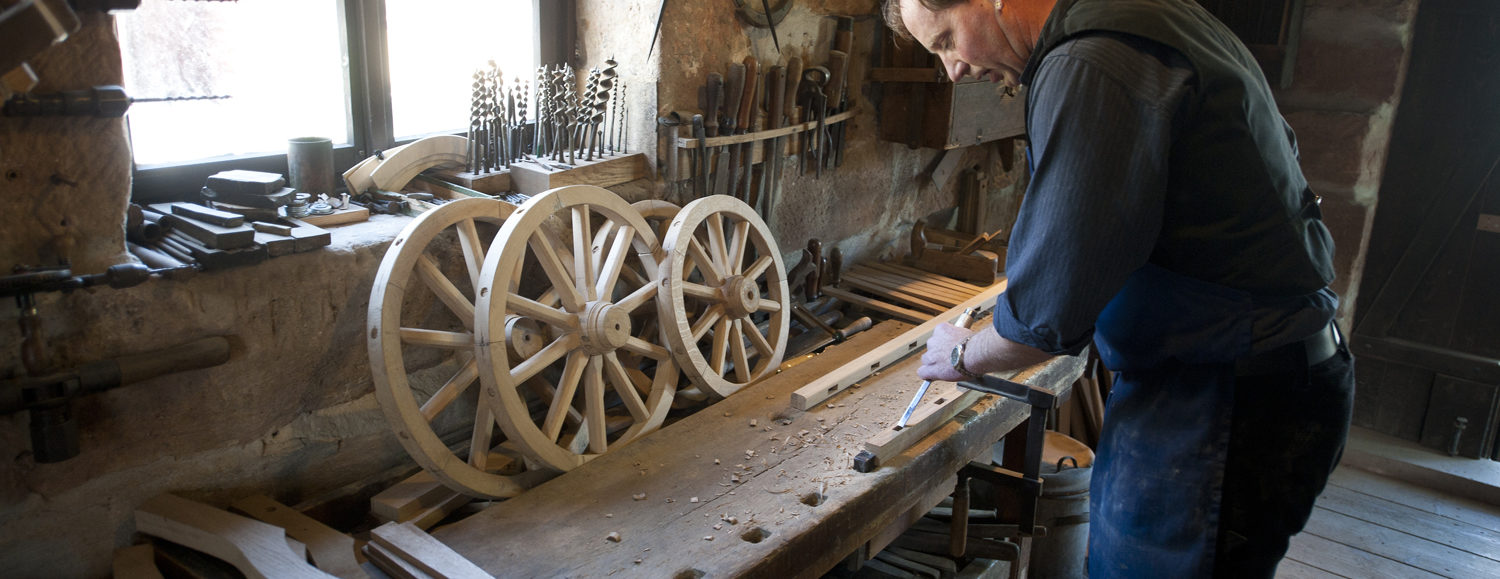
Wheelwrighting and the closely related wainwrighting were common trades in villages up to around 1950. Like the blacksmith, these craftsmen occupied a key position in rural society, as they facilitated mobility. They made wheels, wheelbarrows, handcarts, carts for horses and oxen, sleighs, carriages, and also frames for ploughs and harrows. They furthermore made tool parts, ladders, fence boards and baker’s peels for the bakehouse.
Wheelwrights kept a great variety of wood in store to make wheels which could take the heavy stress of everyday use. For the hub, which was not allowed to split under any circumstance, elmwood was best suited. Wheelwrights used seasoned durable oak wood for spokes. Wheel rims were made of ash, which was durable yet flexible enough.
First, the craftsman would roughly shape the hub from his block of wood, and then he turned it on a foot-operated (later engine-run) lathe. The holes for the spokes were pre-drilled with a brace and bit and finished with a chisel.
The spokes, which had been prepared with an axe and then planed, were finished with a carving knife. Every spoke was given a tenon at one end, which fit snugly into the hub, while the other end was rounded to match the indentations in the rim. Once the rims had been cut and the indentations for the spokes had been drilled, the wheel was ready for assembly. As soon as the wheelwright had finished his wood work, the smith, usually with the wheelwright’s assistance, would lay an iron tyre onto the wheel. This involved heating the prepared iron strip and putting it hot onto the wooden rim. Cooled with water, the tyre would pull the wooden parts together. The wheel now formed a stable unit and was ready for use.
After the end of the 1930s, wheelwrights’ products and services were required less and less; after the Second World War the trade died out.
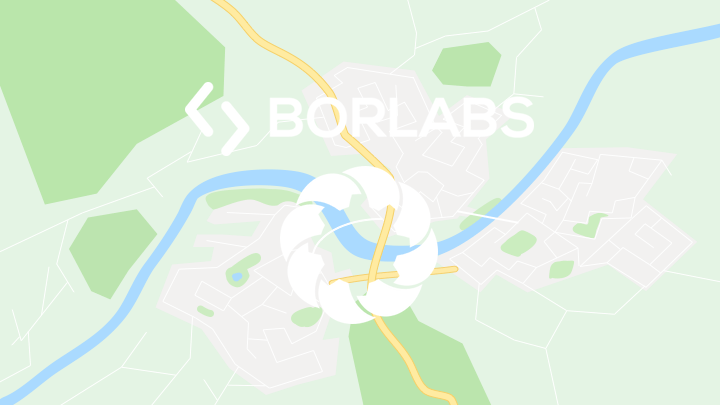
Mit dem Laden der Karte akzeptieren Sie die Datenschutzerklärung von Google.
Mehr erfahren
More links
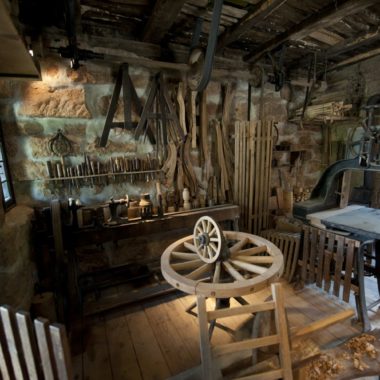